How AI Minimizes Downtime in Manufacturing Operations
Manufacturing downtime is a persistent challenge affecting operational efficiency and profitability. Research indicates that unplanned downtime can cost manufacturers thousands of dollars each hour. This post will explore how AI for Manufacturing technologies, such as deep learning and sensors, minimize downtime and improve logistics through effective inventory optimization. Readers will gain insights into successful case studies and the financial benefits of reducing downtime. By understanding these advancements, manufacturers can address their downtime issues and enhance their overall operations
AI for Manufacturing: Understanding AI’s Role in Reducing Manufacturing Downtime
Downtime in manufacturing refers to periods when a plant’s operations come to a halt, negatively affecting productivity and inventory management. This section will explore how AI tools, such as predictive maintenance software, can analyze engine performance and computer data to forecast potential issues, thereby minimizing disruptions. Insights will highlight the importance of maintaining efficiency in manufacturing processes.
Ready to tackle downtime and optimize your processes? Explore our Process Expert Solution today and take the first step toward seamless manufacturing operations!
Defining Downtime and Its Impact on Operations
Downtime in manufacturing is defined as any period when operations cease, often due to equipment failure or delays in raw material supply. This disruption can severely hinder productivity, leading to losses not only in output but also in consumer satisfaction. The integration of automation and AI for Manufacturing, including natural language processing, allows for real-time monitoring and predictive analytics, which helps organizations anticipate failures in robotic systems and streamline processes, ultimately reducing operational downtime.
AI Technologies That Minimize Downtime in Manufacturing
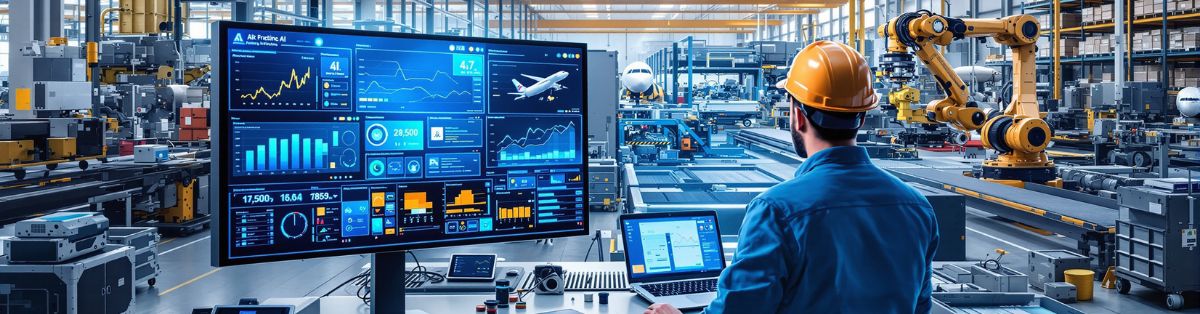
Predictive analytics plays a crucial role in equipment maintenance, enabling organizations to anticipate and resolve issues before they escalate. Machine learning enhances real-time performance monitoring, providing valuable information about operational efficiency. Furthermore, robotics and automation streamline production processes, significantly impacting sectors like aerospace and vehicle manufacturing. Each of these technologies contributes to minimizing downtime, ensuring seamless operations.
Predictive Analytics for Equipment Maintenance
Predictive analytics serves as a vital tool in equipment maintenance by utilizing computer vision and data processing techniques to monitor machinery performance continuously. By analyzing data collected from various internet-connected devices, organizations can proactively identify potential issues, enabling timely interventions before equipment failures occur. This approach not only helps in reducing maintenance costs but also optimizes production efficiency, ensuring that manufacturing operations can run smoothly while maintaining competitive pricing structures.
Ready to revolutionize your operations? Explore The Automated Engineer to unlock the full potential of predictive analytics and SCADA integration for enhanced efficiency and reduced downtime!
Machine Learning for Real-Time Performance Monitoring
Machine learning enhances real-time performance monitoring in manufacturing, directly impacting productivity and minimizing downtime. By analyzing data from various stages of the supply chain, AI for Manufacturing leverages machine learning algorithms to identify patterns and predict potential interruptions in operations. This proactive approach allows manufacturers to quickly address issues, ensuring compliance with industry regulations while maintaining smooth supply chain management.
Robotics and Automation in Production Processes
Robotics and automation significantly enhance production processes within the manufacturing sector by integrating advanced technologies such as machine learning and programmable logic controllers. These technologies streamline operations along the value chain, ensuring consistent quality control while reducing the likelihood of downtime. By utilizing supercomputers for data processing, manufacturers can analyze performance metrics in real time, allowing for timely interventions and optimal productivity levels.
Successful Case Studies of AI Implementations
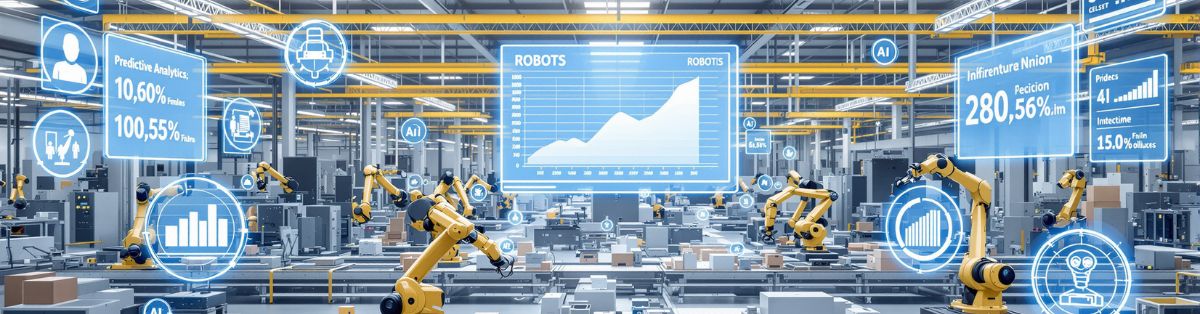
Manufacturing Facility A achieved increased efficiency metrics through enhanced inspection processes and smarter resource allocation driven by AI for Manufacturing. In contrast, Manufacturing Facility B experienced a dramatic reduction in failures, showcasing the effectiveness of AI for Manufacturing in maintaining operational integrity. These case studies demonstrate how language and intelligence technologies can significantly impact revenue and productivity in manufacturing.
Manufacturing Facility A: Increased Efficiency Metrics
Manufacturing Facility A successfully implemented AI algorithms to enhance efficiency metrics by integrating advanced data analysis techniques into their processes. Through consistent monitoring and analysis of operational data, the facility identified bottlenecks that were affecting productivity and customer service. This research-driven approach allowed them to optimize workflows and significantly increase output while reducing downtime, proving the value of AI in manufacturing settings.
Manufacturing Facility B: Dramatic Reduction in Failures
Manufacturing Facility B implemented advanced software solutions, including digital twin technologies, to significantly reduce failures within its operations. By creating virtual models of factory machinery, the facility gained real-time insights into equipment performance and potential failure points, leading to proactive maintenance strategies. This approach not only enhanced sustainability by optimizing resource usage but also improved transport efficiency across the supply chain, resulting in a more resilient manufacturing process.
 The Automated Engineer allows manufacturing companies to more easily analyze their systems and equipment. Pair this with our Process Expert solution and you have a workforce that can stay on top of your SCADA analytics and more quickly troubleshoot issues when they arise.
The Financial Benefits of Reducing Downtime Through AI
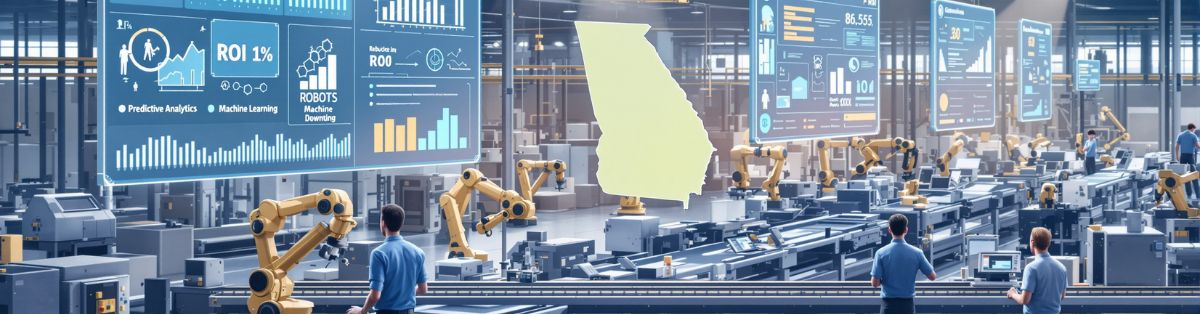
Calculating the return on investment (ROI) on AI initiatives is essential for understanding the financial benefits of minimizing downtime in manufacturing. This section discusses knowledge acquisition, the role of workforce training, and the specifics of demand forecasting. These elements contribute to effective process optimization, particularly for manufacturers in Georgia, illustrating how AI can drive substantial economic advantages.
Calculating ROI on AI Investments
Calculating the return on investment (ROI) for AI for Manufacturing initiatives requires careful analysis of speed and resource allocation. Companies can assess ROI by evaluating improvements in operational visibility through integrated enterprise resource planning (ERP) systems, which connect different functions and enhance decision-making. By quantifying the reduction in downtime and the subsequent increase in productivity, businesses can gain a clearer understanding of how AI for Manufacturing investments translate into tangible economic benefits.
Overcoming Barriers to AI Adoption in Manufacturing
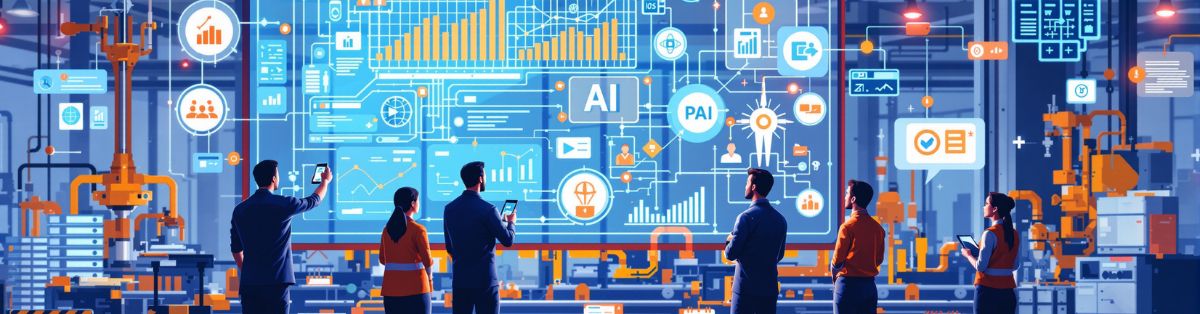
Overcoming barriers to AI adoption in manufacturing is crucial for minimizing downtime. Addressing workforce resistance is essential to foster acceptance of machine learning technologies. Additionally, ensuring data quality and integration enhances forecasting accuracy and decision-making. These elements contribute to effective data analysis and optimize consumption in manufacturing processes, leading to improved operational efficiency.
Addressing Workforce Resistance
Addressing workforce resistance to AI for Manufacturing adoption is essential for harnessing the potential of data science and improving operational efficiency. Effective leadership plays a crucial role in guiding employees through the transition, emphasizing the importance of data quality in enhancing decision-making processes. By investing in infrastructure that supports the integration of Internet of Things (IoT) technologies, organizations can provide training and resources that empower workers, ultimately leading to smoother adoption of AI for Manufacturing solutions and minimized downtime.
Ensuring Data Quality and Integration
Ensuring data quality and integration is vital for successful AI adoption in manufacturing operations. High-quality data enhances the effectiveness of artificial intelligence and machine learning algorithms, enabling businesses to make informed decisions that improve management processes. For instance, implementing SAP as a centralized system can streamline data collection and minimize the costs associated with inaccurate or incomplete information, ultimately leading to a reduction in downtime and increased operational efficiency.
Future Trends in AI for Minimizing Downtime
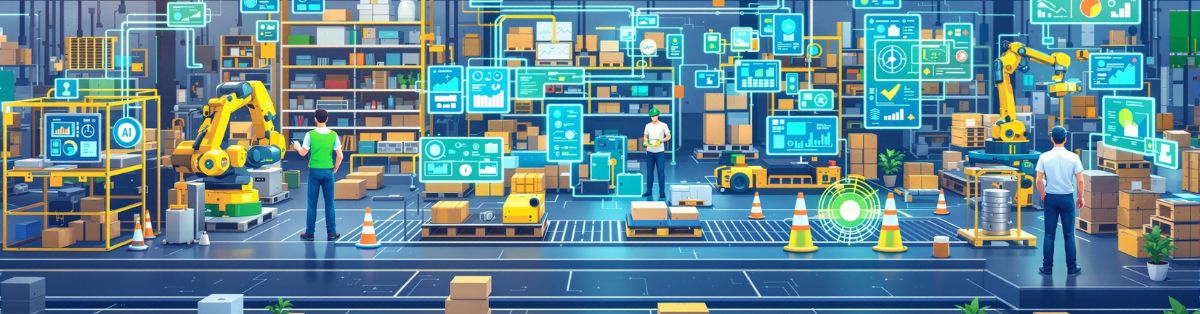
Innovations on the horizon promise to significantly enhance AI for Manufacturing‘s role in minimizing downtime within manufacturing operations. The growing importance of AI for Manufacturing in smart manufacturing emphasizes its impact on optimizations in electronics, energy efficiency, and streamlined warehouse management. These advancements will improve not only operational performance but also the overall customer experience, leading to more resilient manufacturing environments.
Innovations on the Horizon
Innovations in artificial intelligence are set to reshape the manufacturing landscape by enhancing operational efficiency and minimizing downtime. Technologies like our Automated Engineer and our Process Expert facilitate data integration and analytics, enabling manufacturers to create simulations of production processes that identify bottlenecks before they affect outputs. This value proposition not only improves design and production strategies but also enhances the overall customer experience by ensuring timely deliveries and high-quality products.
The Growing Importance of AI in Smart Manufacturing
The growing importance of artificial intelligence in smart manufacturing lies in its ability to facilitate digital transformation by leveraging synthetic data for optimization. Companies can significantly reduce operational risks by employing predictive analytics to anticipate failures and enhance production processes. For instance, AI-driven systems can analyze vast amounts of data to make accurate predictions, directly impacting efficiency and minimizing downtime in manufacturing operations.
Discover how AI is transforming manufacturing! Learn more about implementing AI in manufacturing and its impact on efficiency and productivity by visiting PwC’s guide to AI in manufacturing.
Conclusion
AI for Manufacturing plays a critical role in minimizing downtime in manufacturing operations by enabling predictive maintenance and real-time performance monitoring. Through advanced analytics and automation, AI for Manufacturing enhances operational efficiency, reduces costs, and boosts productivity. The integration of these technologies leads to timely interventions that keep production processes running smoothly. By embracing AI for Manufacturing, manufacturers can significantly improve their competitiveness and overall effectiveness in the industry.